Intelligent control and compact modelling
The efficient operation of high-tech systems requires insight into the condition of their critical components, so that failure – and resulting downtime – can be prevented or at least anticipated. Think of an electric car that relies on the faultless functioning of numerous electronic components and integrated circuits for smooth running. To ensure reliable operation, the remaining useful lifetime (RUL) of such components has to be determined. As direct measurement of this quantity is evidently not possible, procedures have to be found to derive a reliable RUL estimate from the state and the behavior of the components.
A promising approach is digital twinning: making a digital model of the component based on physics and fed with real-life sensor data. Reden explored this approach for estimation of the RUL of an electronic component. The work was conducted within the framework of two European projects, IMOCO4.E and COMPAS.
IMOCO4.E was aimed at providing distributed edge-to-cloud motion control intelligence through a reference platform consisting of AI and digital twin toolchains and other mating building blocks for resilient manufacturing applications. Ultimately, the goal of IMOCO4.E (Intelligent Motion Control under Industry 4.0) was to strengthen European industrial competitiveness.
COMPAS was devoted to compact modeling of high-tech systems for health management and optimization along the supply chain. Simulations are necessary at various stages of the design process to ensure mechanical robustness and reliability. COMPAS aimed to develop novel, compact models and ultra-compact digital twins. The compact models should capture nonlinear, transient and coupled (i.e. multiphysics) situations, while the digital twins should be able to self-sufficiently cast decisions (ultimately in real time) for prognostic health management.
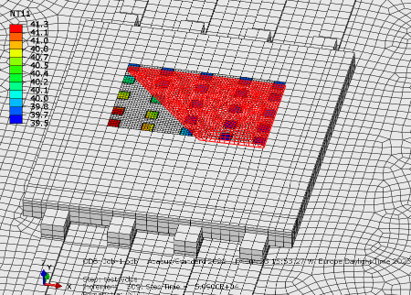
Failure mode evaluation
The concrete case revolved around the RUL of a power switch. Its RUL is determined by failure modes such as delamination due to thermal cycling. When, in this power switch, a die is attached to a printed circuit board that is more compliant, the cyclic expansion and shrink of the die attach will inevitably lead to stresses and ultimately crack formation in their interface. For this failure mode, our challenge was to find a model of the damage evolution based on information of the real-world product. This model could be used to predict the RUL as the time until the damage level exceeds a predefined failure threshold.
Delamination can be described as crack propagation in an interface between two layers. The degree of damage is represented by how far the crack has propagated in terms of the size of the delaminated area. For simplicity, we took this delaminated area as a triangle originating from one corner of the surface of the component under consideration. Crack propagation is driven by the energy release rate and the number of thermal cycles the component has undergone thus far.
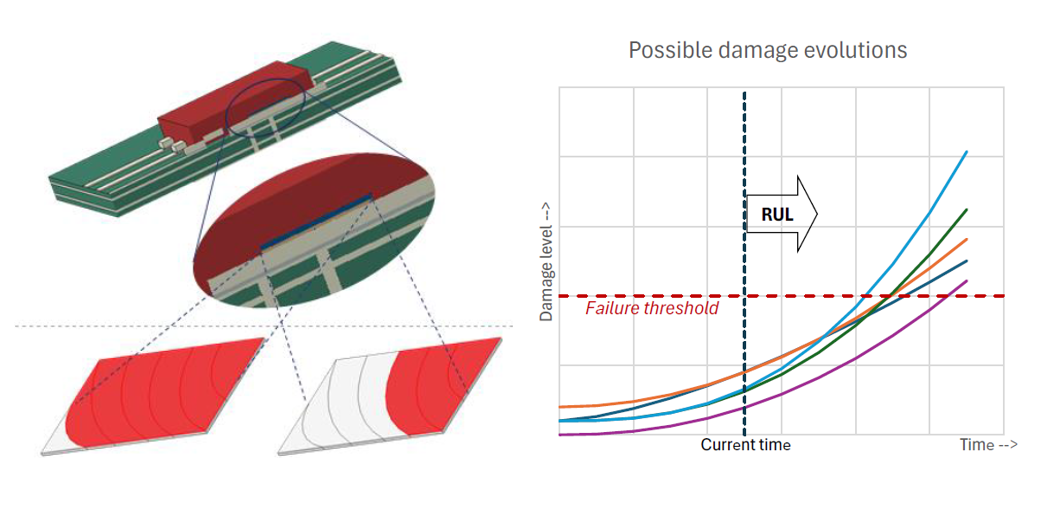
Reduced predictive model
We created a simple and efficient model in which the delaminated area is a function of the energy release rate and the number of cycles. The model has three parameters: the initial delamination area and two interface strength parameters. Due to the temporal evolution of the process, the model features an integral. This simple predictive model was compared with finite-element model (FEM) simulations. We found that the two models showed good agreement up to a damage level of 50%, which served our purpose perfectly, as 50% is well above any meaningful failure threshold.
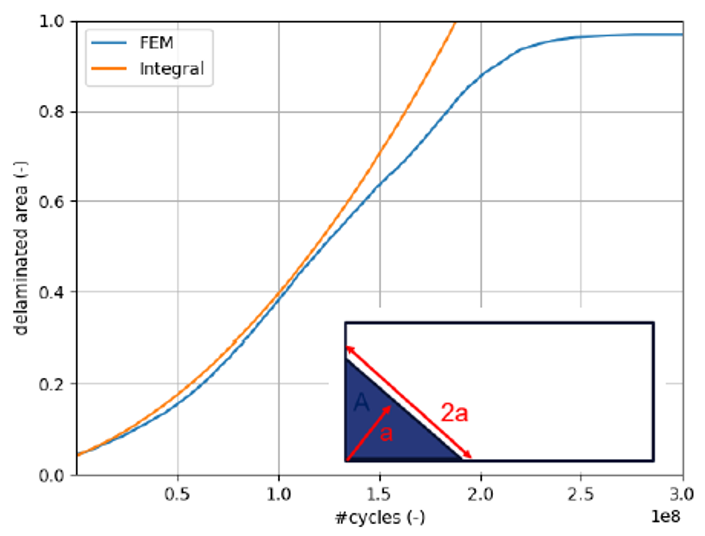
Diagnostic model
As no direct measurement of the delaminated area was available, we had to resort to an indirect measurement to create a diagnostic model. For this purpose, we selected the temperature, as delamination will locally reduce the thermal conductivity and hence influence the thermodynamic behavior of the component. We used the diagnostic model to conduct virtual (FEM) experiments, in which the component was heated at different frequencies and multiple delamination levels. The temperature response showed a clear correlation with the degree of delamination for a specific frequency band. We translated these results into a virtual sensor, i.e., a function that relates temperature to delamination.
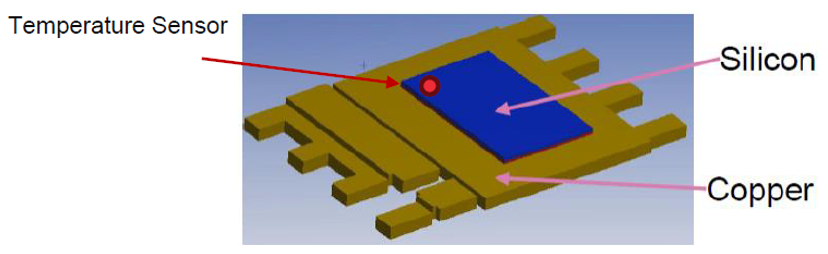
Machine learning
The diagnostic model, however, was too time-consuming for practical applications, so we needed a reduced model. We combined the predictive model and the diagnostic model in a digital twin that used experimental sensor input to run multiple simulations. The results served as input for updating the parameters of the predictive model by way of machine learning.
Learning on the job
A digital twin should represent a ‘real-time’ condition of the component in the ‘real world’. The predictive model therefore needs to learn what the condition of the product is, as represented by the diagnostic model. Machine learning is used to ‘learn’ its critical parameters. Sensor input from experiments is then used to determine the state with multiple simulation runs. This sensor data is later also used to update the state of the diagnostic model.
The reduced model can then be used for the intended application, the real-time monitoring of the condition of the component to estimate its RUL. The estimation comes in the form of a stochastic distribution, from which the RUL is derived as the time at which there is a 95% probability of no failure beforethe component is replaced.
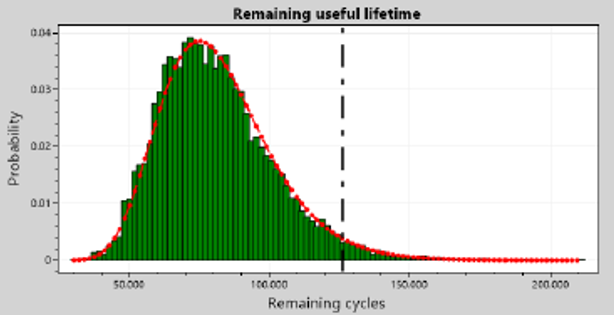
Generic framework for digital twinning
This project clearly showed the power of digital twinning. To exploit its potential, the framework that we created for testing and optimizing the digital twin of the electronic component was of a generic nature. We can now use this framework to accelerate the development of digital twins for all kinds of modelling, monitoring and optimization applications.
