Introduction
Smit Draad in Nijmegen, the Netherlands, is a leading cable manufacturer. Its largest product group, CTC (Continuously Transposed Conductor) cables, is used for the production of power transformers. The market trend in power transormer design is to downsize transformers, while at the same time optimizing their power. To achieve that, transformer manufacturers need big CTC cables (> 43 strands) with small winding diameters and short pitches. Cable manufacturers need to adjust their transposing head technology in order to be able to produce CTC cables that meet that need.
Transposing quality is key
For winding cables on smaller cores, the distance between bends needs to be shorter. The key parameters of the transposing process are:
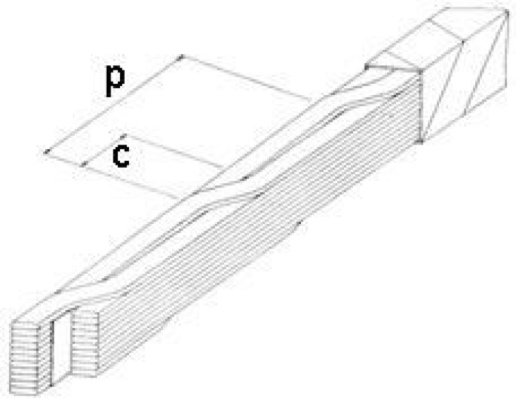
p = pitch = transposing distance
c = cross over length
Transposing Factor = pitch / strand width
Crossover factor = c / strand width
In one turn on the winding diameter all strands need to change their position one step:
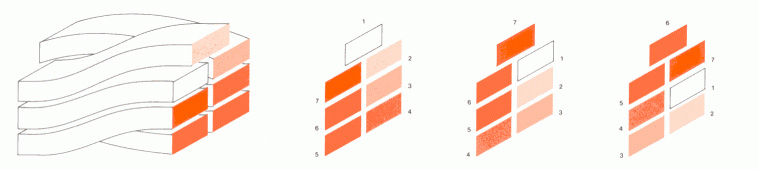
During the winding process stress is being built up, potentially affecting the transposing quality – and thus the manufacturability – of the CTC cable. Reducing the transposing factor to 5 x strand width leads to less stress during the transposing process and a better cable:
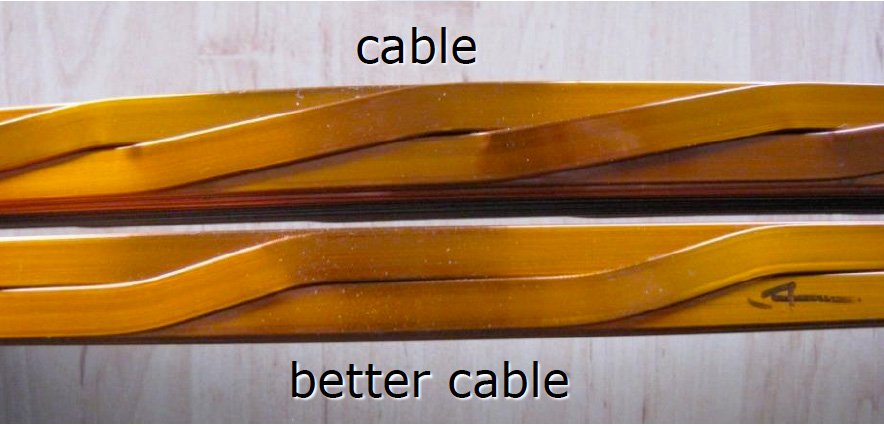
The challenge
As there were no commercially available transposing heads that could reach the target factor of 5 x strand width, Smit Draad had to either upgrade its current transposing head or develop an entirely new transposing head.
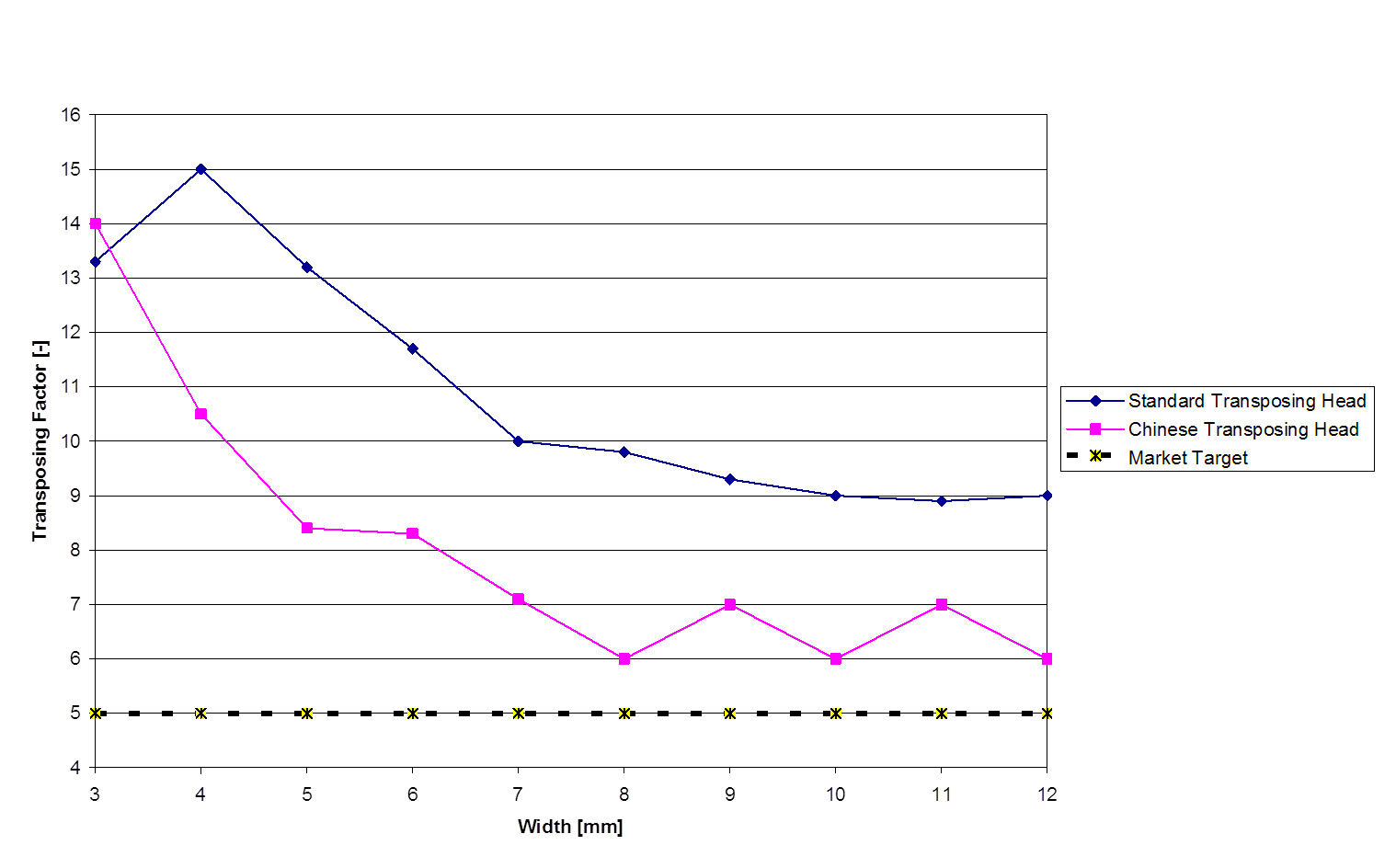
The upgraded or newly designed tranposing head had to comply with challenging requirements:
- Capable of many bends (over 167 million a year)
- Transposing factor 5, in order to wind cable on a smaller transformer core
- Strict dimensional and material tolerances on the cable
- Insulation of wires in the cable must be PERFECT
- Copper deformations upto maximum material limits
- Concept of transposing head based on product (cable)
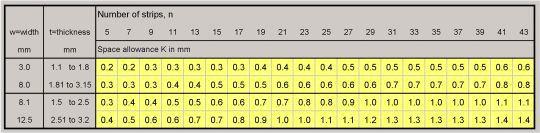
Our approach
Using our multi-physics based modelling and simulation approach, we started out building a model on relevant inputs (geometry of strands and cable, material/copper hardness, transposing factor) to simulate the process results (loading/unloading, displacements, stresses/strains, deformation behaviour).
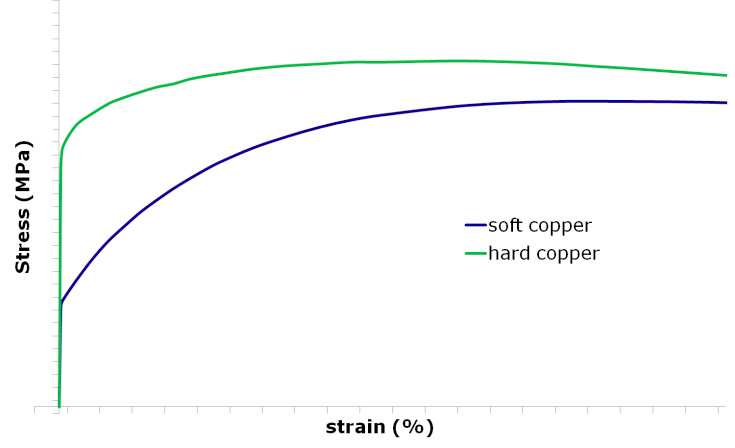
Through simulation of the process and validation of the model, we gained a thorough understanding of the relationships between the design parameters and the performance of the transposing process – and then captured that understanding in a broad set of knowledge rules. With these in mind, we optimized the design parameters of the model to achieve the desired product performance.
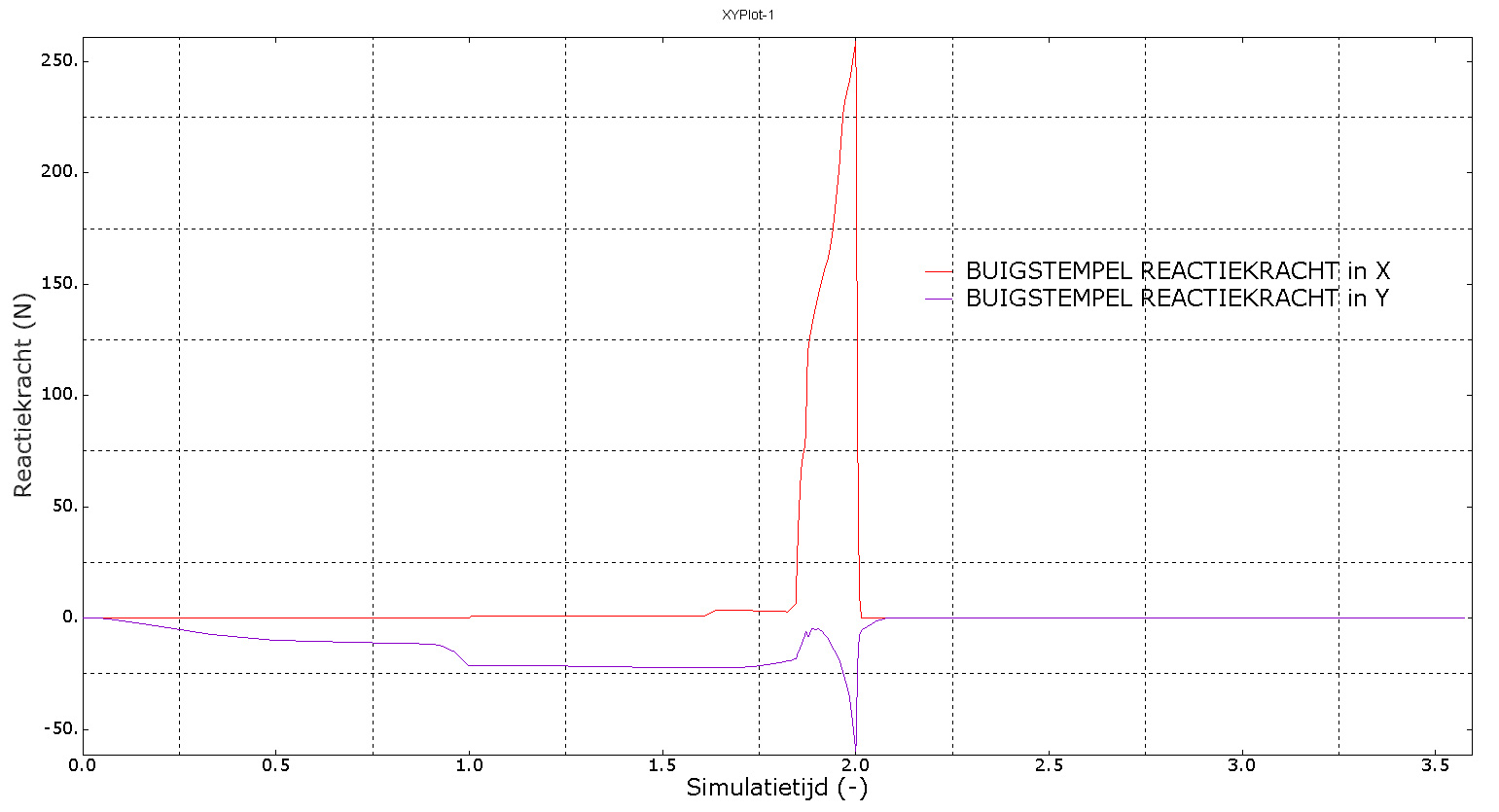
Variations for thicker strands…
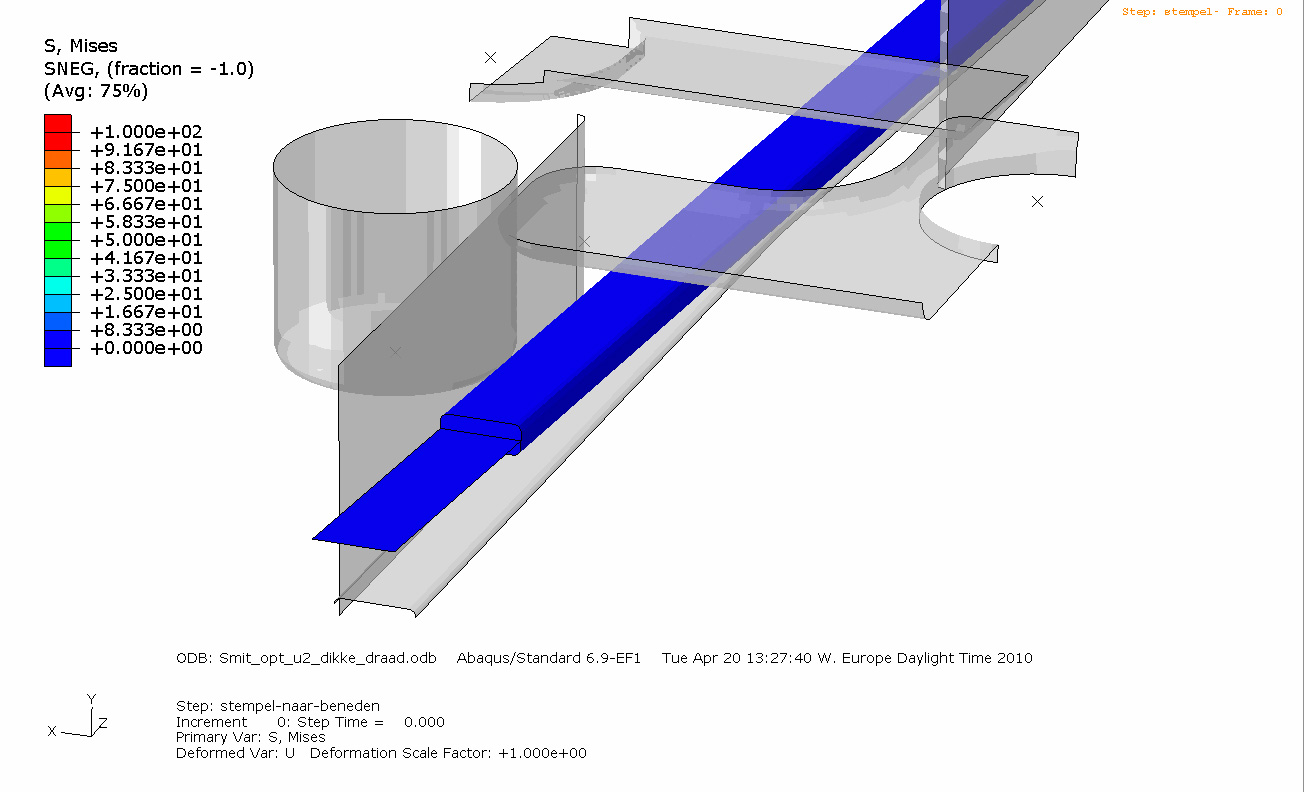
…or harder copper:
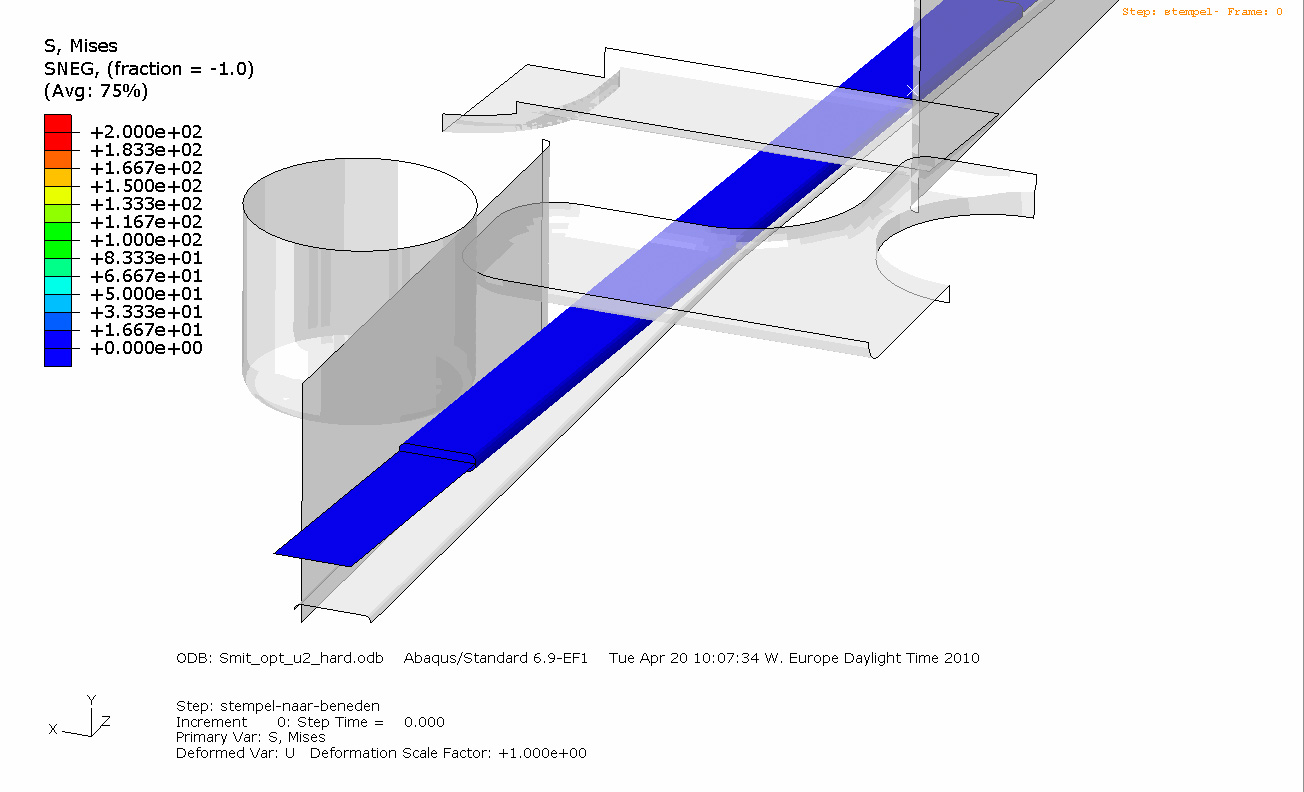
The first yield: a completely virtual test concept
After establishing all relevant knowledge rules we built a completely virtual test concept that would allow us to explore the full potential of design space, for new solution directions in:
- the number of strands
- the hardness of copper
- strand dimensions
- tooling dimensions
By running numerous virtual tests we mapped the impact of all variations in – for example – strand thickness and cable dimensions.
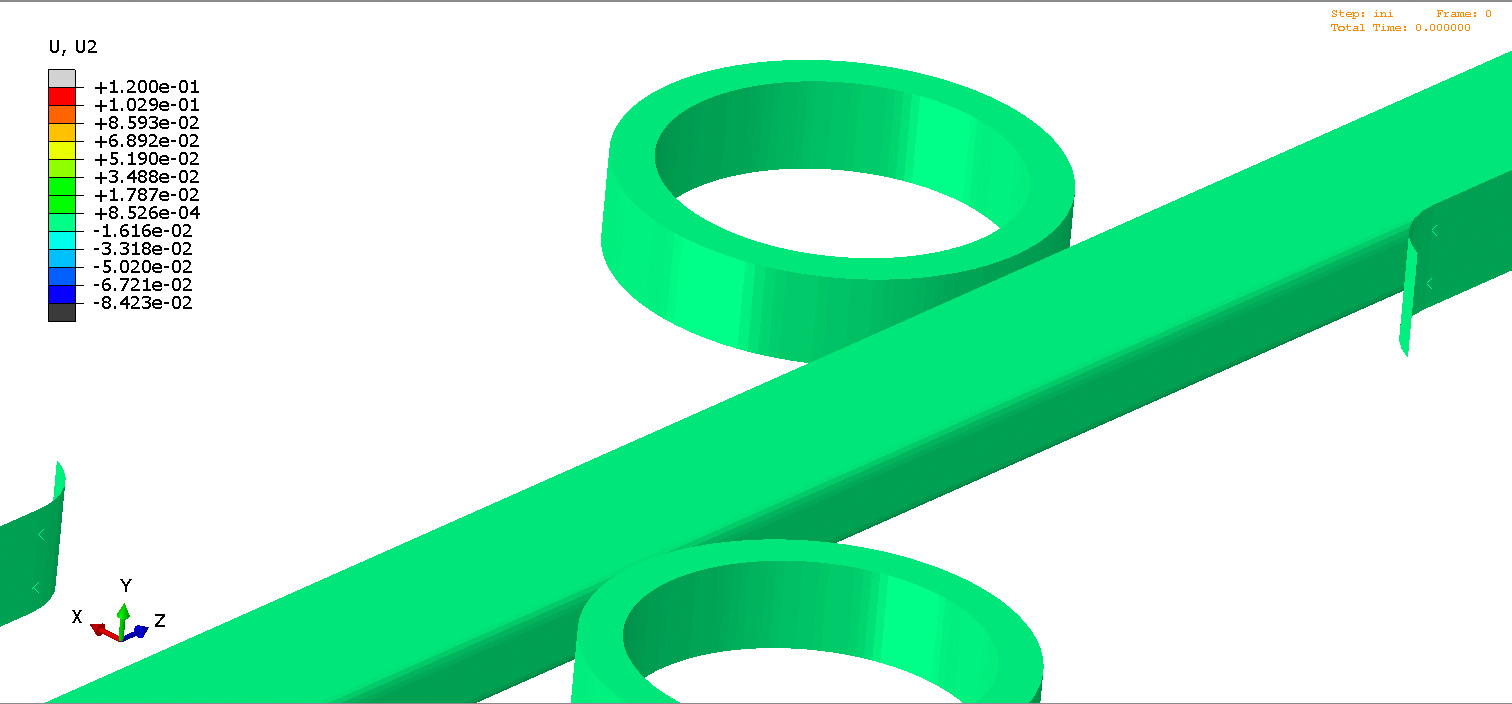
Due to the local compression of the bending tooling, an increase of thickening and a change in cable dimensions may occur, causing the strand to bulge:
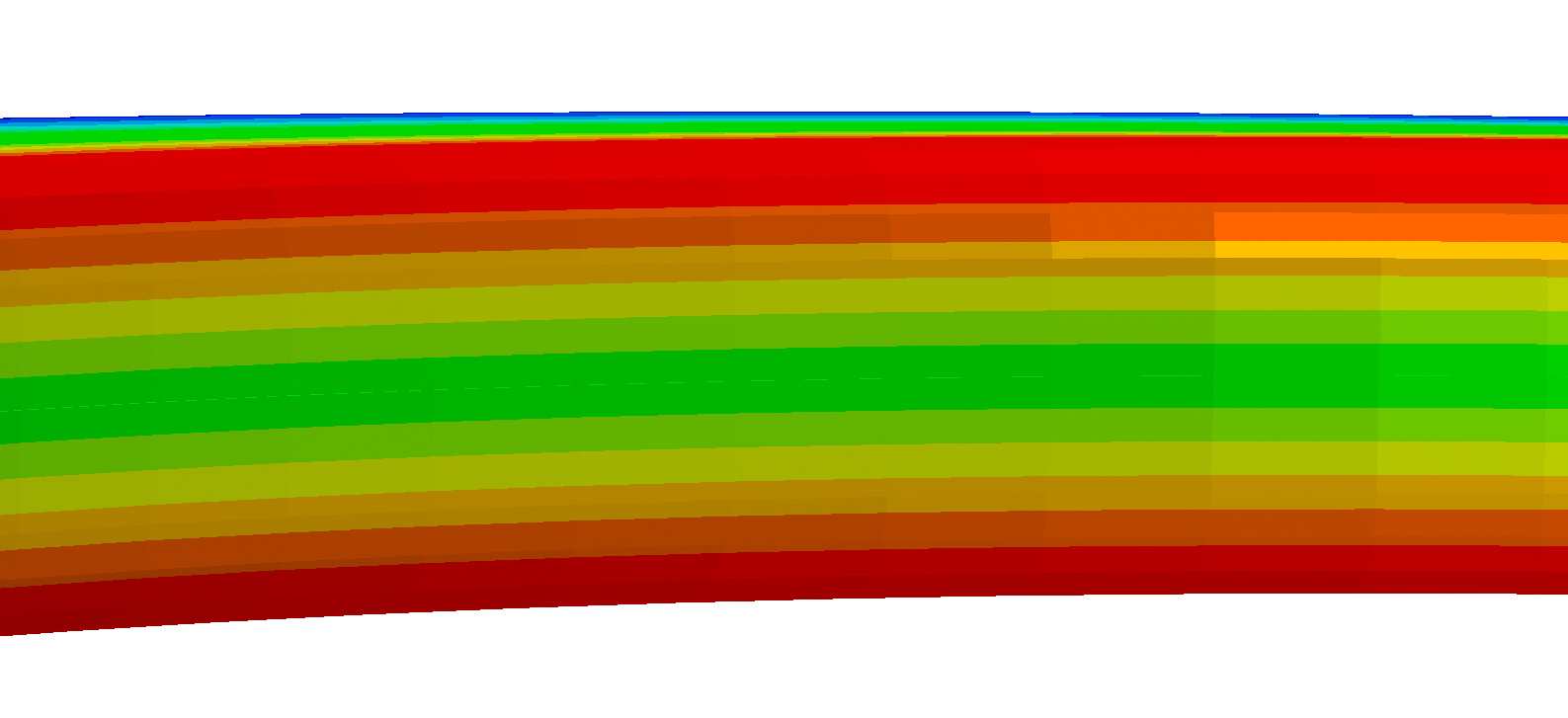
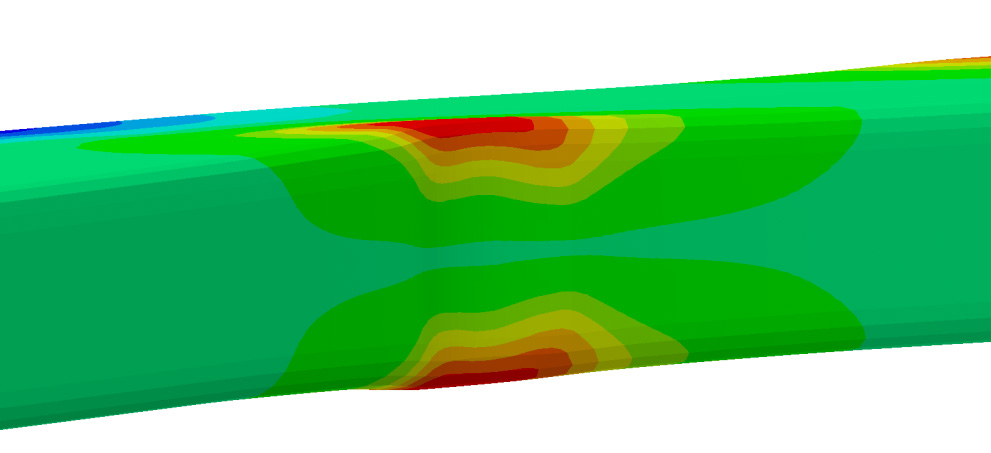
Based on the outcomes of the virtual test concept we defined a new set of design rules for an improved machine concept:
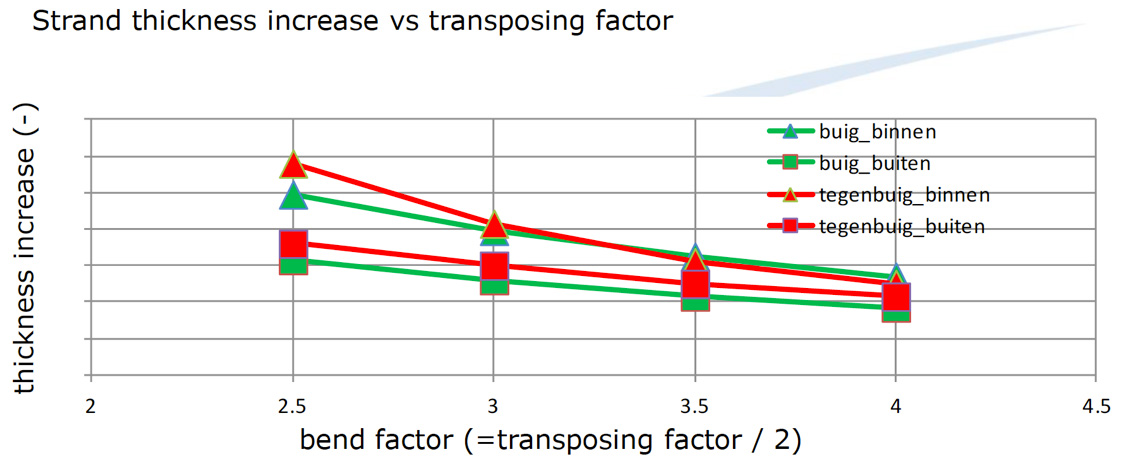
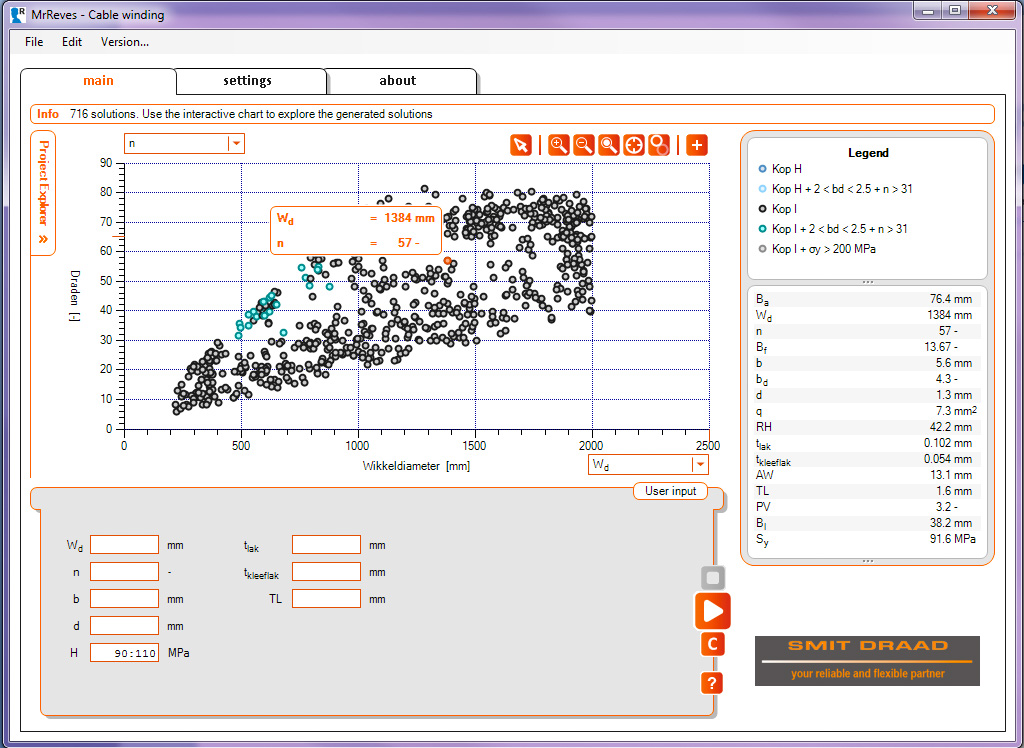
Results and final deliverables
It appeared that an upgrade of the current transposing head would achieve transposing factor 6, whereas the target factor was 5. Therefore Smit Draad decided to develop an entirely new transposing head, using the insights from design space exploration and the new design rules derived from the virtual test concept. We delivered the design for the new transposing head to the machine builder, after which it was built and implemented in the production process.
Summary roadmap Transposing Head Development
2010 Development of simulation models for making cable
Validation against current transposing heads (Standard and Chinese head)
2011 Improve current heads up to limits of their capability
Design new concept for transposing head
2012 Implementation of newly developed concept (machine building)
2013 Installation in production process