Holistic design
Skin is one of the most challenging multi-compound materials in product design. For products such as razor blades and medical instruments that interact with the human skin, product performance and quality depend on the mechanical skin-product interaction. This can be studied with multi-level skin modeling as part of the complete Computer-Aided Engineering (CAE) process chain. The holistic design of product functionality and the associated manufacturing processes requires detailed knowledge of the local material behavior and the seamless transfer of information such as material models between the various CAE stages.
Reden performed skin modeling simulation studies as part of use cases in the European projects VMAP (Virtual Material Modelling in Manufacturing) and UPSIM (Unleash Potentials in Simulation). The VMAP project was aimed at creating a common understanding and interoperable definitions for virtual material models in CAE and ultimately achieving an open, vendor-neutral interface standard for the exchange of material, measurement, sensor and simulation data. The UPSIM project took this one step further by creating a safe environment for companies to collaborate on simulations in a repeatable, reliable and robust manner and to implement simulations in a credible digital twin setting.
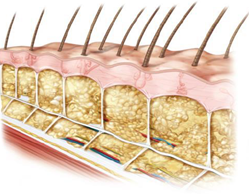
Complex biological system
Skin is a biological multi-layer system that performs multiple functions, such as protection against the outside world, regulation of heat and moisture, and tactile sensing. From outside to inside, it comprises a dead corneum layer, a living epidermis containing nerve ends, hair, etc., a dermis with ligaments of collagen and elastin, and a fatty hypodermis. The skin is fed by blood vessels and exhibits complex behavior, such as folding and wrinkling, partly determined by the interaction with external objects. For example, roughness decreases with increasing strain exerted on the skin, while stiffness decreases with increasing length scale as demonstrated by indenter tests. Skin properties vary with a person’s age and health condition, and environmental factors such as humidity.
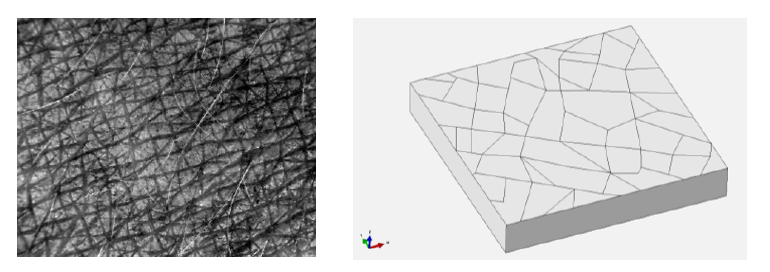
Model building and validation
Reden created a skin model as a multi-layered solid with different material properties for each layer. Surface texture was incorporated in the model following a unit-cell-based approach that was adopted to reduce computational effort. The unit cell measured 5 mm x 5 mm with a depth of 1 mm, covering the dermis, epidermis and corneum layer. As many parameters were involved, various tests were required to create meaningful material fits. Material properties were fitted from in-plane tensile tests and out-of-plane compression tests, while maintaining the correct wrinkling behavior and incorporating the size effects on stiffness.
One example was the doming test. Doming is the upward swelling of the skin under suction. Experiments were carried out on the skin of a test person’s forearm with the Aramis high-resolution optical 3D measuring system for determining the 3D strain field resulting from the suction action. The experimental results for principal strains of up to 10% and doming heights of 3-4 mm were used to validate the skin model.
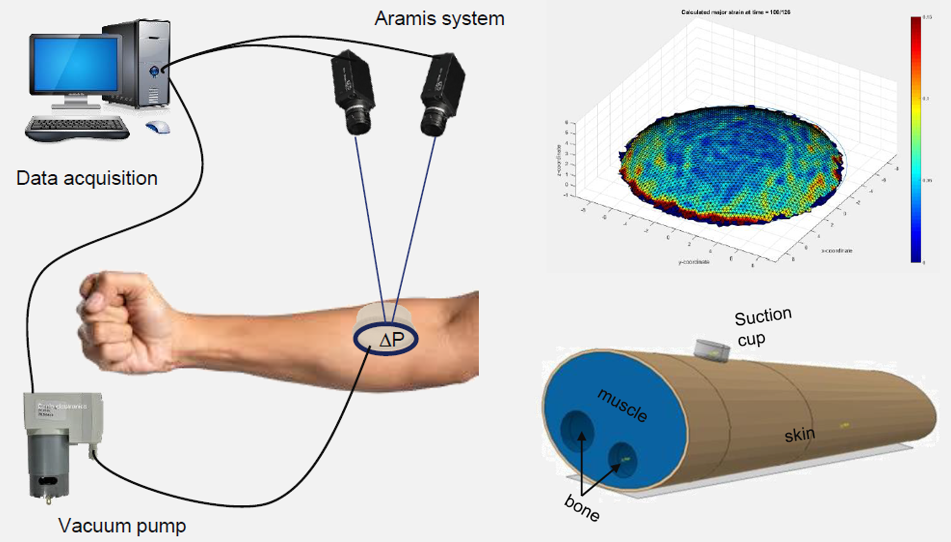
The scale issue
As a concrete use case, the design of hybrid plastic-metal products such as the Philips OneBlade razor was studied. Here, the focus was on the interaction between the skin and the razor blade moving over it with a certain skin pressure distribution of the product.
Besides skin model complexity, the issue of scale also posed a challenge. In the dynamic region near the moving blade a kind of bow wave is created, locally leading to large deformations in the skin. In this interaction zone, a detailed geometry is required to obtain a correct representation of the mechanical skin behavior. For this, the model has to be ‘micro’, i.e. with fine mesh.
On the other hand, a large skin model volume is needed to account for correct boundary conditions. In the static region, far from the blade, the model can be ‘macro’, with a coarser mesh. This leaves modeling the transition between the two regions a challenge in its own right. All-in all, four orders of magnitude have to be covered, from 0.01 mm to 100 mm.
Combining the two requirements leads to extremely large simulations and long run times. The solution that we adopted was starting with a coarse (locally refined) model and applying either coarsening of refining steps where applicable, to account for an object moving over the skin during the simulation. The timing of these coarsening/refining steps turned out to be a crucial factor.