Getting a grip on sailboats
Sailboats are exposed to diverse and extreme wind conditions. To determine the stresses and shape of the sail it is practically impossible to test every scenario in real life. When questioning the impact of wind speed, rigging pre-tension, sail material and/or boat design, virtual testing is the answer.
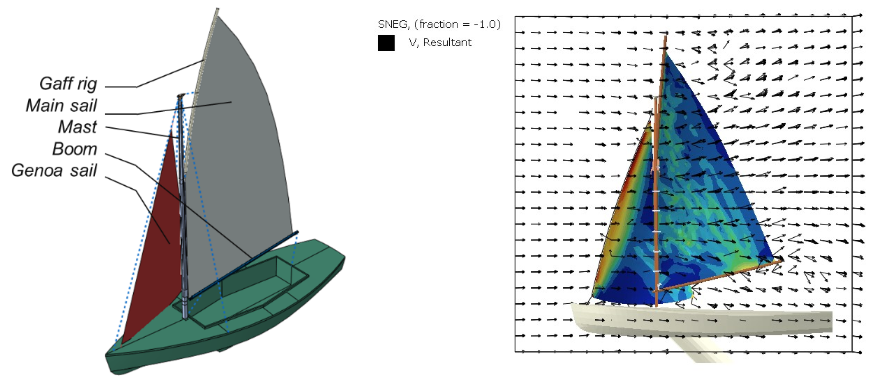
Finding the balance
The forces exerted by the wind and the shape of the sail are closely linked. This imposes a challenge, because everything on the boat is deformable: the sail and rigging stretch, and the mast, gaff and boom bend. A fluid-structure-interaction (FSI) coupling offers the solution.
An analysis on a Valk has been performed in close cooperation with Van Oossanen, whom provided the geometry of the Valk and its sails. The air flow was modelled using a potential flow solver, and together with the mechanical (finite element) model, pressure and deformation data is continuously exchanged, untill a steady-state solution is obtained.
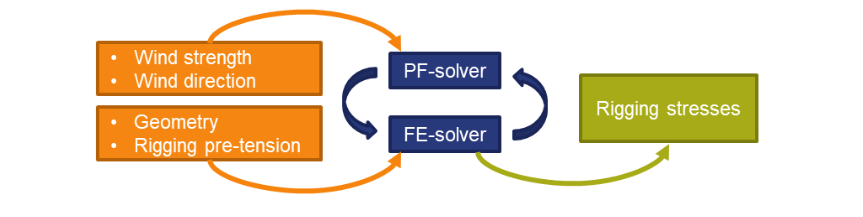
The last link: the real world
The last step is to build our confidence in the model, which is provided in the form of experiments in cooperation with our partners in the RoSF project. The sails material was tested at NHL Stenden, providing the required input for the material modelling in the mechanical domain. The resulting sail deformation has been validated with 3D optical measurements by Hanze (Lidar), on a Valk provided by Molenaar at the Workumer Jachthaven.
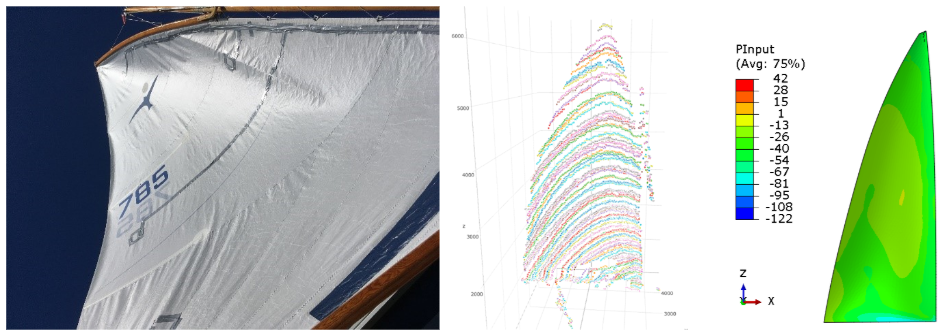